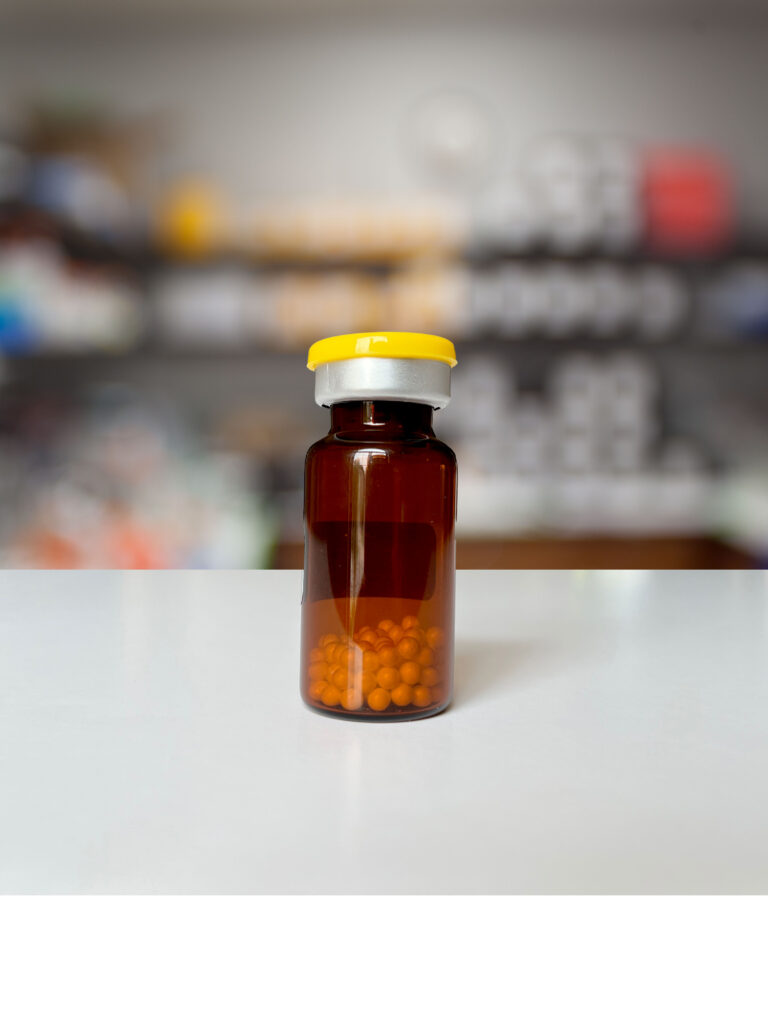
Lyophilization is a process designed to remove water from a sample or product through a controlled freezing and vacuum application. The method leverages the triple point of water, where solid, liquid, and gas phases coexist under specific temperature and pressure conditions. The result is a room temperature stable product that is much lighter than the original sample or product.
The Lyophilization Process
The Lyophilization process typically involves three phases:
Phase 1: Freezing
In the first phase, the sample or product is frozen with cryoprotective excipients in a freezer or freeze-dryer. During the freeze-drying process, the excipients serve as a protective barrier and help preserve the long-term stability and efficacy of the product. Rapid freezing below the triple point, typically at -40 degrees Celsius, prevents the formation of large ice crystals that could damage structurally sensitive materials, like cells.
Phase 2: Primary Drying
The second phase of lyophilization involves reducing the pressure below the triple point of water to create a vacuum. The vacuum aids in sublimation, while a cold condenser simultaneously traps and solidifies the water vapor. Next, a gentle application of heat energizes the solid ice crystals, causing them to sublimate. About 95% of the water in the product or sample is removed during this process, resulting in a mostly dry cake. This can be a slow process, as careful heat control is crucial to preserve the material’s structure.
Phase 3: Secondary Drying
This final phase removes residual unfrozen water molecules through desorption. A slight temperature increase breaks the bonds between water molecules and the frozen material, releasing the ionically-bound water molecules. The result is a lyophilized cake that is lighter than the original product or sample.
The Benefits of Lyophilization
Lyophilization offers many benefits across various industries, such as:
- Preservation of Biological Activity & Improved Stability. Lyophilization is especially beneficial for preserving the biological activity of sensitive materials, such as proteins, enzymes and vaccines. The gentle freezing and drying process in lyophilization minimizes the risk of loss of activity or damage to these sensitive compounds. This is crucial for substances that are prone to degradation or structural changes when exposed to traditional drying methods.
- Stability at Ambient Temperatures. The removal of water prevents chemical reactions that can lead to product degradation, resulting in a product that is stable at ambient temperatures. An ambient temperature stable product reduces the need for controlled temperature storage and shipment. The product can be stored and distributed globally without the need for dry ice or refrigeration. A lyophilized product can be particularly advantageous for products that need to be distributed to regions with challenging temperature conditions.
- Ease of Use. Lyophilized products can be formulated in an “all-in-one” format that can reduce an error-prone, multi-step process to a simple “reconstitute and go” process.
Fit-for-Purpose Lyophilized PCR Amplification Assays: Everything You Need in a Single Bead
Performing lyophilization in-house can be challenging and often is not feasible for many organizations. Lyophilization of a PCR amplification assay must begin with lyophilization-compatible reagents. Standard, off-the-shelf, PCR reagent formulations commonly contain ingredients like glycerol, certain salts, or detergents that inhibit lyophilization. Therefore, the identification of a PCR master mix formulation that is lyophilization compatible and retains its functionality is a critical first step. Additionally, lyophilization of a high performing PCR assay can be a complex, empirical, and time-consuming process. Precise control and optimization of the lyophilization conditions and excipients is required to yield a uniform, easily resuspended, final lyophilized PCR assay.
A Fit-for-Purpose Lyophilized PCR Amplification Assay from Promega is designed to simplify and expedite the development of a lyophilized PCR assay specific to customer needs. By utilizing our lyophilization-compatible PCR reagents you can quickly identify a lyo-compatible master mix formulation that meets your performance requirements. This streamlines the transition to pilot lot production to verify post-lyophilization PCR performance. Once the lyophilized PCR assay performance is verified, seamlessly transition into final production under a certified quality system.
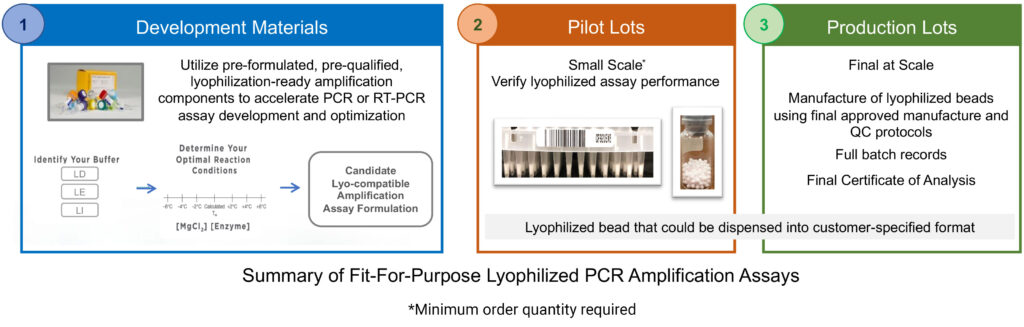
Key Features:
- Everything You Need in a Single Bead. Each individual bead contains all the necessary reaction components–all you need to do is add your sample. This not only saves time but also increases consistency and reliability by reducing the potential for human error.
- Adaptable Format. The beads can be easily scaled to meet any reaction volume and are adaptable for various applications as manufacturing needs evolve.
- Flexible Dispensing Options. The beads can be dispensed into nearly any customer-specified format, such as bottles, 96-well plates, and 8-well strip tubes.
- Easy Integration for Sample-to-Answer Assays. The bead format allows for easy integration into the design and manufacture of sample-to-answer diagnostics.
- Ambient Storage. Reactions are stable without cold-chain transport or storage.
- Lyophilization Partnership Process. At Promega, we support our customers through the entire development, verification and production process of a lyophilized PCR amplification assay, offering a comprehensive service from product conception to delivery.
Learn more about our custom capabilities by contacting our Custom and OEM Manufacturing team or by visiting our Custom Capabilities page.
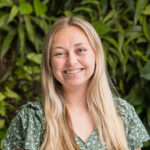
Sara Christenson
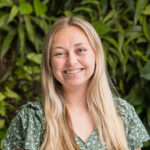
Latest posts by Sara Christenson (see all)
- Cracking the Undruggable Code: Top 10 Key Takeaways - December 10, 2024
- An Introduction to Lyophilization: Process, Benefits & Possibilities - March 5, 2024
- COVID-19 and Type 1 Diabetes: Exploring the Potential Link - November 16, 2023